Wet Electrostatic Filter
Frederick Cottrell developed the first wet electrostatic filter (WESP) in 1907 to control sulfuric acid fog from a copper smelting process in Pinole, California.
Since then WESP technology has been well used in industrial and utility applications around the world to remove dry insulator ESP, submicron particles, condensate vapors and acid mist. The wet washer cannot capture sub 0.3 micron particles due to its small size.
Description
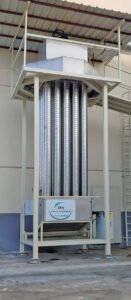
Wet Electrostatic Filter
Frederick Cottrell developed the first wet electrostatic filter (WESP) in 1907 to control sulfuric acid fog from a copper smelting process in Pinole, California.
Since then WESP technology has been well used in industrial and utility applications around the world to remove dry insulator ESP, submicron particles, condensate vapors and acid mist. The wet washer cannot capture sub 0.3 micron particles due to its small size.
Configuration
A WESP can be configured with flat plate collection electrodes that handle a horizontal gas flow similar to a dry ESP. Alternatively, a WESP can be configured in an upstream tubular configuration above the wet scrubber to minimize waste.
WESP Configuration
Collection tubes can be round, square, rectangular or hexagonal. Our company offers WESP designs in both plate and tubular form.
Our company can offer multiple modules fully assembled into the chimney or field installation. can supply WESPs in modules. Planned for larger installations and depending on site costs and ready to install, shipped to site.
Yield
WESP filtration efficiency depends on several parameters; gas velocity, collection surface area, corona power, and electrically, a WESP can be configured in an upstream tubular configuration above the wet scrubber to minimize waste.
Place
A WESP is typically installed after an ETİ MADEN wet flue gas sulfuric acid system or after a wet scrubber in an industrial application where the flue/process gas is cooled to moisture saturation. After cooling, the gaseous pollutants condense to form submicron aerosols that can be captured within the WESP. WESP can be integrated into the washing unit (right) or placed after the washing unit.
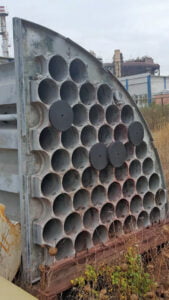
Operation
A Wet Electrostatic Filter (WESP) operates in the same three-step process as a dry ESP;
1- Charging the incoming particle with negative ions from the corona formation using a high voltage system.
2- Collecting the negatively charged particle on the positively charged collection electrode surface.
The main difference between wet ESP:
3- Cleaning of the collected particle by water sprays, irrigation or condensation or detachment or condensation against sonic horns on the collecting electrode surface.
Technology Features
- Performance – Above 90% typical and up to 99% possible.
- Compact Size – minimizes space and cost.
- Cleanliness – can be reduced from 10%.
- Reliability – rooted technology in hundreds of applications.
- Fuel Flexibility – allows using a variety of fuels to reduce fuel cost.
- Multiple Contaminant Control – submicron solids, condensables and sulfuric acid mist.
- Modular Design – allows scaling up to any size airflow.
- Maintenance – no moving mechanical parts; continuous self-cleaning.
- Pressure Drop – Typically less than 1 bar than WESP.
Construction materials
Due to the saturated conditions of the process, WESPs are susceptible to corrosion. Appropriate selection of building materials depends on analysis of the process gas, expected pH and chloride levels in the water. The building material can range from carbon steel, stainless steel, to high-end alloys such as Uranus B6 and Lead. Every industry and plant site is unique. Zen Electro Filter always continues its R&D studies for a suitable building material that provides long life, corrosion resistance and reliability.